Manufacturing Work Order Template
A manufacturing work order is a form used in supply chain management for scheduling specialty production orders as requested by a customer. The form is used to permit production to begin and contains details on what is to be made, the dimensions/specifications of the product(s), and the costs (both direct and indirect) that will need to be paid upfront or after production is complete.
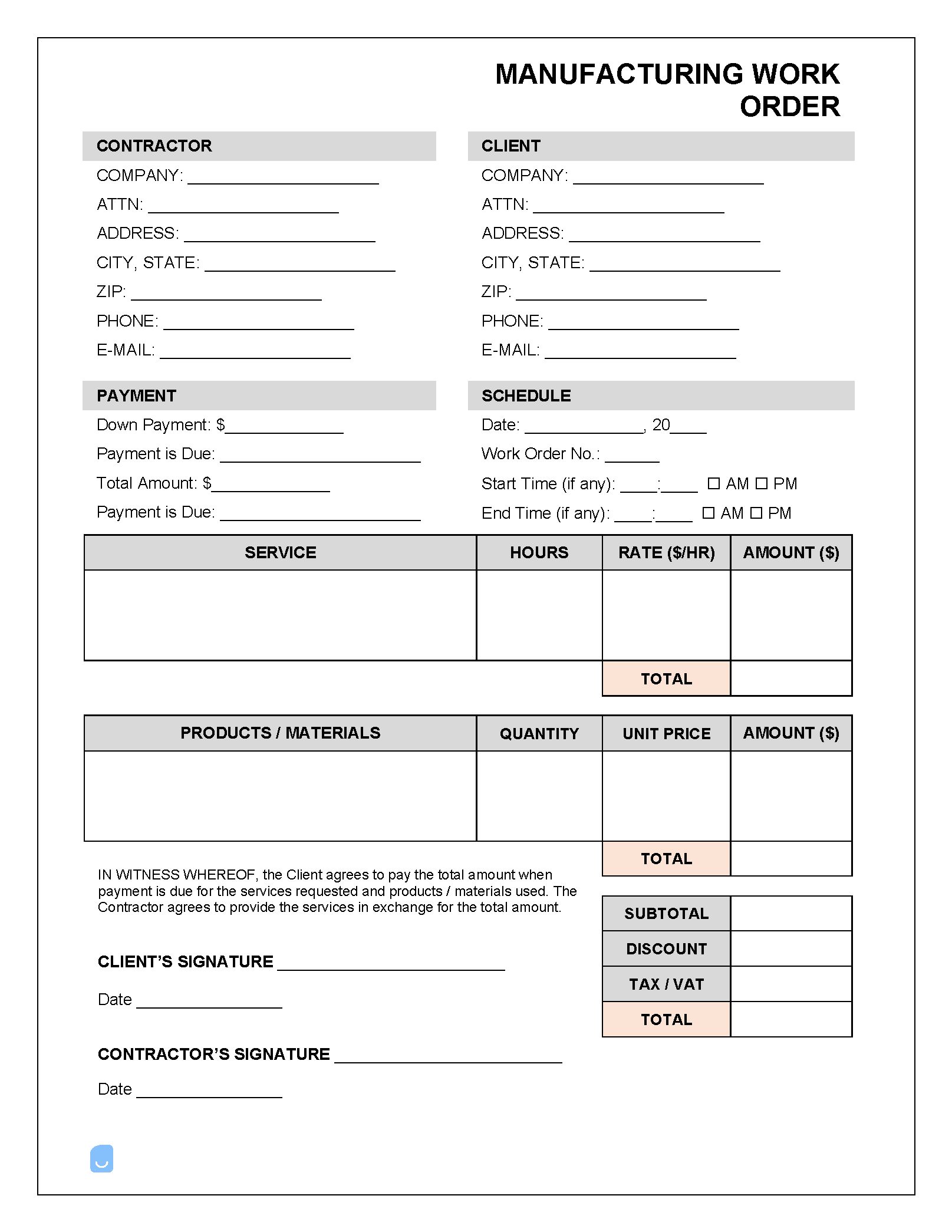
How to Use a Manufacturing Work Order
Work orders outline the process for how a client’s production request will be completed, beginning to end. In manufacturing, it is rare that the client will complete the work order on their own due to the in-depth information required. Instead, a client will complete a sales order, which is a relatively basic form that provides enough information to allow a supervisor to create the work order. In order for a work order to be effective, it needs to allow for the following to be recorded:
- Work order number
- Date created, work start date, and expected completion date
- Client information
- Product(s) requested, along with total quantity, pictures, dimensions, models, etc.
- Material/part numbers, quantity, unit cost, inventory (if any)
- Any notes or important considerations
- Signature of the client and/or the manager
Benefits
Manufacturing companies benefit from digital work orders in several ways, as it:
- Gives companies a means of scheduling employees in advance – reducing the likelihood of over-staffing.
- Materials and parts can be ordered ahead of time, keeping operations on schedule.
- It serves as a paper trail, should the job need to be referenced in the future.